MANUFACTURING CHALLENGES
If you are like most manufacturing leaders, you’re familiar with the continuous pursuit of becoming more productive while meeting a large list of requirements.
– Enhance worker safety and environmental compliance
– Improve product quality
– Reduce costs
– Increase supply
– Shorten lead times
– Optimize inventory
– Retain key employees
– Battle inflationary increases in raw material costs
– Reduce energy and water usage
The list of demands continues to grow in both length and complexity as the global landscape evolves to include new factors such as inflationary costs in raw materials, never-ending supply chain disruptions caused by transportation delays and material availability issues. You are not alone in trying to navigate these compounding challenges.
A major component of success, often ignored, is a practical, science-based framework tailored to your business.
THE IMPACT OF AUTOMATION AND DIGITIZATION
To meet their challenges, most companies are investing heavily in digitizing their operations. They are busy implementing Enterprise-wide Requirements Planning (ERP) software systems and deploying new factory automation tools. Many are the CEOs and operations leaders who have spent millions of dollars on new technology and continuous improvement efforts only to see disappointing results. Key terms like Industry 4.0, Supervisory Control and Data Acquisition (SCADA) systems, Smart Factory, Machine Learning, Artificial Intelligence (AI), Factory of the Future, and the Internet of Things (IoT) are now common vocabulary in manufacturing industry groups. Over the past decade many manufacturing and distribution companies have gone through lengthy and expensive ERP deployments.
These technological advances have been layered on top of continuous improvement methodologies like Lean, Six Sigma, and Agile to name a few. Over the past 10 years US manufacturers have expended millions of dollars and countless worker hours training their staff and transforming their organizations to meet the ever-increasing demands for better quality, lower costs, and improved customer service. According to a report by Allied Market Research, the global ERP market was valued at $35.81 billion in 2018 and is projected to reach $78.41 billion by 2026, growing at a CAGR of 10.2% from 2019 to 2026. This suggests that there has been a steady increase in the adoption of ERP systems across various industries, including manufacturing, over the past decade and the spending is expected to continue. Another report by the McKinsey Global Institute estimated that the manufacturing sector could see a potential economic impact of $4 trillion to $6.2 trillion per year by 2025 through digitization and the adoption of Industry 4.0 technologies.
Overall, it is clear that the US manufacturing industry is investing significant resources into digitization initiatives, with a focus on leveraging emerging technologies to improve productivity, efficiency, and competitiveness.
However, investment in technology has been going on for years without significant effects on productivity.
ELUSIVE PRODUCTIVITY
The US Bureau of Labor Statistics latest report on US Manufacturing labor productivity over the past 10 years shown below indicates that, despite these large investments in ERP deployments and factory automation, true year on year productivity remains elusive.
TIME TO FOLLOW THE SCIENCE
What if there was a scientifically validated methodology to ensure investments in technology result in improved productivity?
In the late 1980s and early 1990s two industrial engineering PhDs, Mark Spearman and Wallace Hop, from Northwestern University’s Master of Management in Manufacturing (MMM) program developed a scientific set of behaviors that could be mathematically modeled and predictably managed to control manufacturing productivity and outcomes.
Spearman and Hopp held bachelor’s degrees in physics and this physics mindset provided them with a different view on manufacturing. Rather than working primarily from complex mathematical formulations to analyze operations as is typical in the field of operations research or subscribing to productivity improvement initiatives that often are very imprecise in application, Spearman and Hopp started looking for the fundamental laws and relationships that governed the behavior of operations much as the laws of physics, e.g., E = mc2, govern the universe. Their goal was to provide operations workers, managers, and executives with accurate understanding and intuition about operations behavior to ensure sound decision-making.
OPERATIONS SCIENCE – REACT LESS, LEAD BETTER, IMPROVE MORE
Operations science focuses on the interaction between demand and transformation and the variability associated with either or both. Operations science defines the set of buffers (inventory, capacity, and time) required to synchronize demand with transformation. This portfolio of buffers and variability drives customer service, cost, and productivity.
That there is general confusion about operations science is easy to demonstrate. Following is a sample of responses (typical for any company where the poll has been conducted) about a couple of vital operations science relationships.
For people in operations, this akin to widespread disagreement about how the law of gravity works or it would be like one or two rowers rowing in opposition to the others. How much more productive are organizations with everyone pulling in the same direction?
While operations science sprang out of the original Factory Physics approach, decades of experience applying the concepts across companies and industries led to the universal framework of operations science. In 2021, Edward Pound founded the Operations Science Institute to advance operations science in operations management with the goal of eliminating chaos, confusion, and waste caused by lack of awareness and understanding of the science governing operations.
The Operations Science Institute’s mission is to build and expand the concepts as a general science. The goal is elimination of widespread waste in operations and, thereby, enable breakthrough success for organizations. Most importantly, the aim is to provide easy access to training and clear understanding of the concepts to allow companies and organizations to be more productive.
The institute does not sell operations analysis and control software or management processes or methodologies. The institute simply teaches and coaches the scientific relationships between key operations parameters. Decades of experience has shown that it takes much more than providing an organization’s employees with cutting edge software to drive consistent productivity. Experience has shown that people need to internalize the principles of operations science in their own work environments to take full advantage of the technology they employ. This is best accomplished with training and education coupled with hands-on coaching from subject matter experts who have successfully implemented the concepts in the workplace. Training, education and coaching are the keys to achieving breakthrough success in improving customer service and productivity. The idea is the same as expressed in the proverb “If you give a person a fish, you feed them for a day. If you teach a person to fish, you feed them for a lifetime.”
The general applicability of operations science has been re-enforced through demonstrated success in widely varying industries including manufacturing, healthcare, product development and construction to name a few. Since the framework has been established as a general science, the concepts apply to all industries.
Operations science builds the foundational understanding of how operations are governed. With this foundation firmly in place, other continuous improvement activities like the Smart Factory, Artificial Intelligence, Internet of Things, Business Analytics, Lean, Agile, Six Sigma, and Theory of Constraints can be layered on top of this foundation to drive additional improvements in business performance and productivity.
The key to optimizing team performance starts with a common language, a clear understanding of the key success drivers, and their relationships to each other. If manufacturing and supply chain operations are vital to your business, the fundamentals of operations science are your key to solving stubborn operational issues. The concepts will enable your people to better utilize your existing technology and provide productivity improvement breakthroughs.
Armed with operations science, your team will be able to implement sustainable solutions and truly deliver the productivity improvements your organization desires using your technology.
At an international medical equipment manufacturer, application of the concepts resulted in a 30% increase in throughput in three months. The examples of success are numerous and span many industries.
If you are ready to react less, lead better, and improve more, contact the Operations Science Institute to advance development of your people and overcome your manufacturing challenges using your existing technology.
Encourage and inspire employees and sustain your operations success over the long term with a common language and operations management grounded in operations science. No software or consulting required. Contact us at the Operations Science Institute and get started on the road to long-term success.
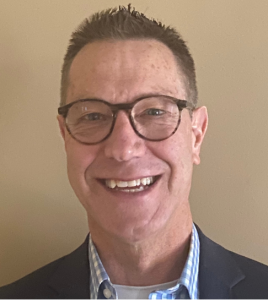
Mike Gores is a senior advisor at the Operations Science Institute. Mike has thirty-eight years’ experience successfully driving continual improvement in Manufacturing, Quality, Product & Process Development and Global Supply Chain Operations. Mike has applied operations science concepts in various leadership positions ranging from product and process engineering supervision, plant quality manager, plant operations manager, process development and product development manager and global manufacturing manager.