The 3M Privacy Solutions Business had a major problem from huge increases in backorders. The division had invested millions of dollars and used all the latest production planning and distribution technology.
Technology was not the problem. This is a common occurrence. Managers tune their systems through years of tweaking and then the business changes. Privacy Solutions needed a quick resolution to resolve the service problems. This area of the business was getting lots of attention within the company. Senior executives were asking not only how this happened, but most importantly how fast could the business turn this around? The added pressure from upper management lead to contentious meetings between operations, supply chain and the sales organizations. Fast resolution was paramount to avoid getting additional “help” from Executive Management.
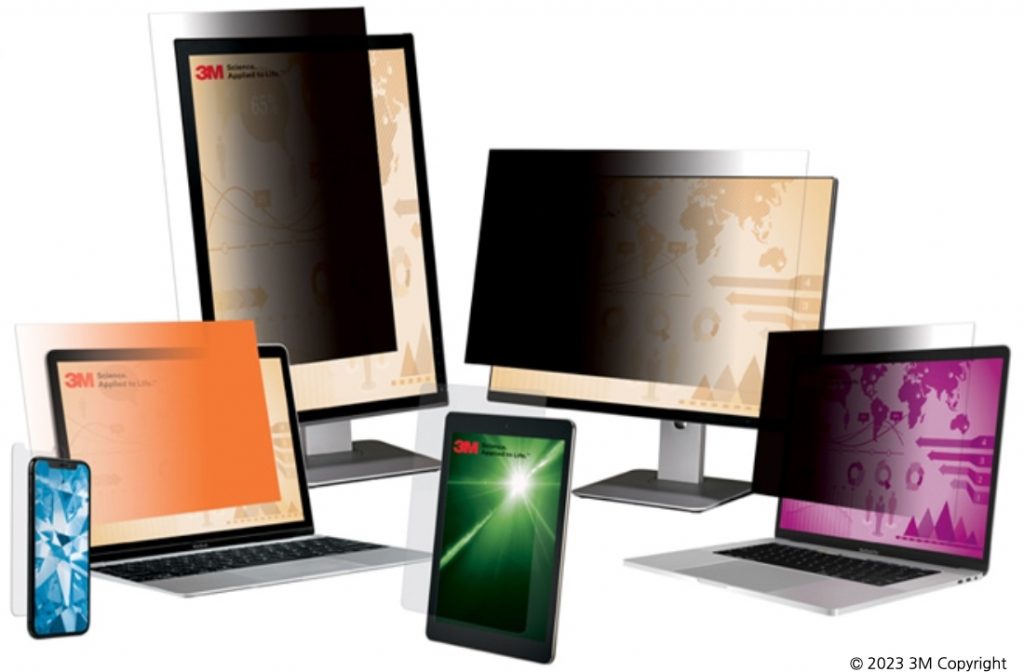
Privacy Solutions provides display screen security devices for computer laptops and monitors. The product is sourced from one main manufacturing facility located in the USA and distributed globally through regional distribution centers.
Privacy Solutions Business was experiencing a significant increase in volume for its product. The go-to-market strategy for the sales team changed to an increased focus on major resellers and large OEM and corporate accounts. This resulted in a significant shift in customer order patterns, larger orders, and less frequent orders. Over a three-month period this created a five-fold increase in backorders for the manufacturing plant. In response, the business had to sink massive effort into production order prioritizing and expediting. Customers were becoming increasingly unhappy which required a similar increase in customer support effort by the global sales team.
Operations science provides a fundamental and comprehensive understanding of operations behavior. When problems occur, the science-based approach quickly pinpoints the how and why of operations performance. Employing an operations science approach, the manufacturing and supply team investigated the root cause of the increase in backorders.
Operations science showed that production scheduling was driving performance out of control due to incomplete calculation of utilization and other well-intended but wayward actions. At the same time, supply planners were not properly setting the planning parameters in the expensive ERP inventory management software. Comparing current practices with the standard operations science framework, the team determined that the manufacturing set up times and product rework times were not being adequately factored into the utilization on key production equipment. The variability in process yields had also climbed with the increase in demand.
Using operations science calculations, the team discovered the utilization was well over 95% and the cycle time was dramatically higher than the lead times the plant was using in its scheduling software. These increases in cycle times had not been communicated to the global supply planners and they were quoting the previous, shorter lead times to customers. This was the root cause of the increase in backorders.
The plant management and business leadership teams were informed of the root causes for the deterioration in performance and a new cross functional tiger team was formed. The tiger team immediately began working to change preventive maintenance activities, operator staffing and shift arrangements to reduce the utilization of key manufacturing equipment. The Quality team members also began root cause analysis into the variability that had increased the rework.
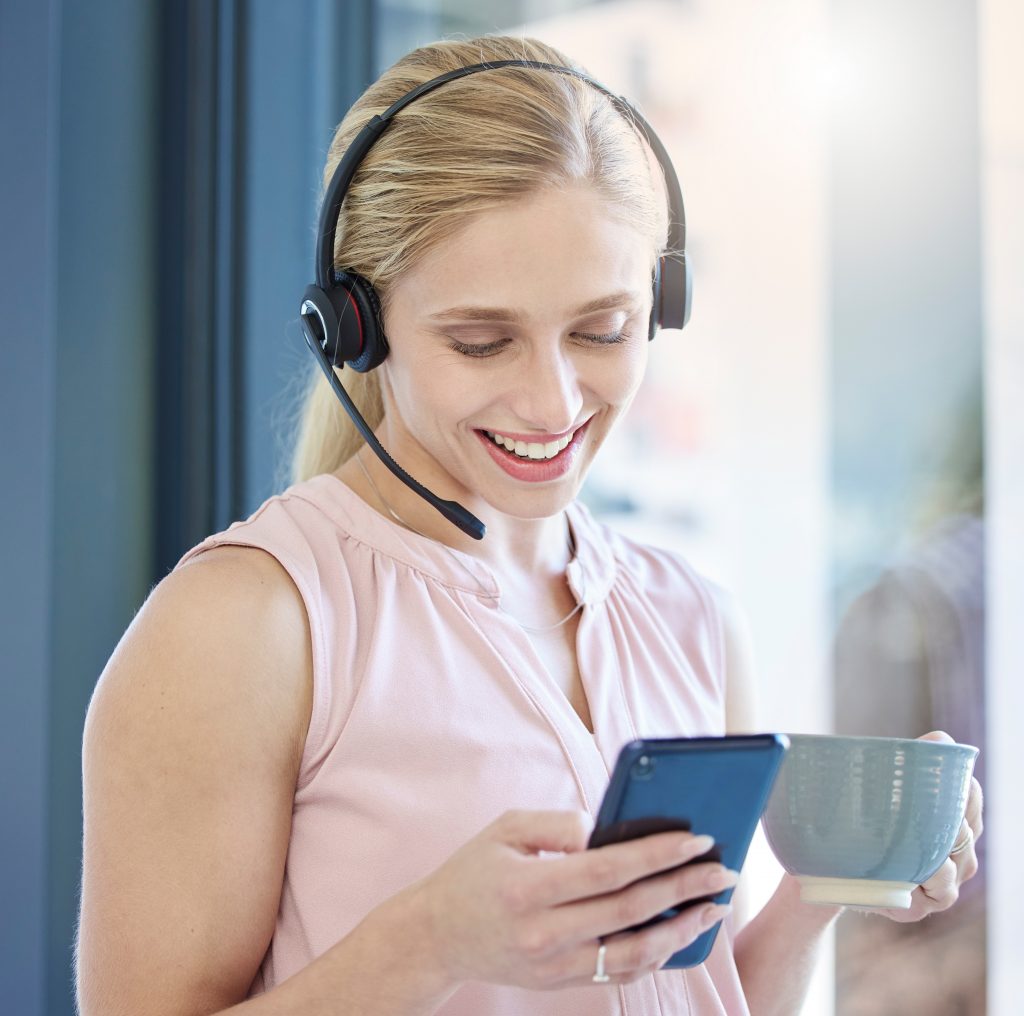
Over a 120-day period the team was successful in reducing rework, improving equipment unplanned downtime, and increasing staffing and shift arrangements to reduce utilization and drive cycle time back to acceptable levels. No new investment in ERP or planning software was required to correct performance.
In fact, this is a common result of good application of operations science. Most facilities already have the software and technology resources needed to improve performance. The investment in those resources is much less productive than when used in combination with operations science.
The plant changed the metrics they were monitoring in their Lean Manufacturing Tier Review process to include rework, unplanned downtime, and key equipment utilization as leading indicators to ensure the backorders were maintained at levels acceptable to the Privacy Solutions business team. They also implemented a weekly tier process with the business team and the global supply planners to ensure all planning parameters were monitored and sustain high levels of customer service and business performance. Problem solved.
Encourage and inspire employees and sustain your operations success over the long term with a common language and operations management grounded in operations science. No software or consulting required. Contact us at the Operations Science Institute and get started on the road to long-term success.